Construir un sistema de escape de motocicletas personalizado
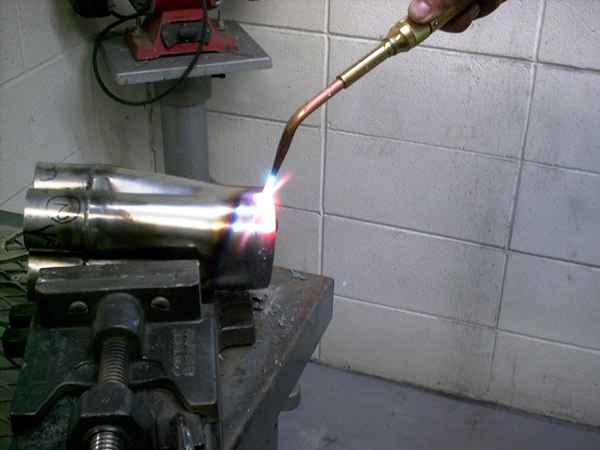
- 1945
- 471
- Sra. María Soledad Acuña
No hay nada más agravante para un constructor de motocicletas personalizado que descubrir a la mitad de un proyecto que el sistema de escape de stock no se ajusta, y no hay ninguno disponible para esta bicicleta en particular. En este punto, la solución obvia es construir un sistema de escape personalizado. Claro, se necesita mucho trabajo y algunas habilidades especiales, pero incluso sin experiencia en el sistema de escape, una mecánica competente puede crear un sistema que sea la envidia de todos los propietarios de bicicletas de acciones.
Una nota sobre el tamaño
Tocaremos brevemente aquí en el diseño del sistema antes de entrar en el método real de fabricación. Sin embargo, los puntos más finos del funcionamiento de un sistema de escape están fuera del alcance de este artículo. Antes de comenzar a diseñar el diseño y comenzar la compilación, debe investigar la teoría y el diseño de sistemas de escape para diversas aplicaciones (desde cilindros individuales hasta 4 hasta 1s). Es importante recordar que cada sistema es único y no "de talla única se ajusta a todos."Además, la modificación de un diseño de escape de stock generalmente afectará la jetting, por lo que es bueno tener algún conocimiento de la sincronización del motor también.
Consideraciones de diseño
Transferencia de calor: Obviamente, un motor en funcionamiento producirá calor. Este calor se transferirá al aire que fluye sobre él, o a cualquier cosa que se acerque a él, por ejemplo, la pierna de un jinete o un carenado de fibra de vidrio. Si es posible, debe evitar envolver la tubería para proteger el área circundante, ya que esta es generalmente una solución temporal al problema básico de un diseño deficiente. También debe permitir la transferencia de calor hacia atrás y el flujo del aire enviará calor hacia atrás, lo que puede ser peligroso si una línea de freno o un componente similar está en línea con la parte trasera de la tubería.
Autorizaciones: Los sistemas de escape deben tener suficiente espacio libre para permitir la expansión y el movimiento. La cantidad de expansión dependerá del rendimiento del motor (más potencia es igual a más calor) y el material del que se hace. El fabricante debe permitir una expansión de tamaño alrededor de la tubería de encabezado de aproximadamente el 20 por ciento.
Complejidad: El viejo adagio para "mantenerlo simple" se aplica mucho a los sistemas de escape. Las tuberías complejas y en constante cambio y los radios de esquina cerrada afectarán negativamente el rendimiento y se debe evitar cuando sea posible.
Estampación: Si bien es probable que no tenga una máquina computarizada de doble flexión, eso no significa que aún no pueda construir un sistema de escape eficiente y atractivo. Sin embargo, algunas herramientas básicas serán necesarias e incluyen lo siguiente:
- Una sierra para hackear de calidad con nuevas cuchillas específicas de acero inoxidable
- Archivos (planos para extremos de tubo y redondos para tirar tubos dentro de los tubos)
- Soldador MIG o TIG (para unir las diversas partes)
- Vicio para sostener tubos durante el corte (necesitará mandíbulas redondas para sujetar uniformemente)
- Herramientas aéreas
Poniéndolo
Teniendo en cuenta todas las pautas anteriores, ahora debe conocer el diámetro y la longitud del sistema que está buscando producir. La siguiente fase es configurar el diseño básico. Inicialmente, puede usar una tubería flexible, como las que se encuentran en una aspiradora, para diseñar su forma básica. Una vez que haga eso, continúe el sistema con varillas de soldadura de aluminio. Uno de los métodos más simples y baratos de establecer un sistema es usar varillas de soldadura de aluminio (1/8 "o 3 mm de diámetro) y algunas arandelas de guardabarros del diámetro exterior correcto del sistema propuesto. En esencia, dará forma a la varilla de soldadura para correr desde el puerto de escape hasta la apertura del silenciador (suponiendo que se utilizará un silenciador, a diferencia de una tubería directa). El cable de aluminio se formará para dar las curvas óptimas (manteniéndolas al mínimo para no interferir con el flujo de gas) y las lavadoras se utilizarán para garantizar que haya suficiente espacio libre alrededor del motor, etc.
Sin embargo, antes de comenzar a dar forma a la varilla de aluminio, marque la longitud óptima de la varilla cuando aún esté recta. La varilla de aluminio debe fijarse a la cabeza del cilindro en la brida del tubo de cabezal y luego en forma para seguir el contorno deseado hacia el silenciador (donde está instalado).
Construyendo el sistema
La siguiente fase es cortar varias piezas de tubos de acero inoxidable para caber sobre la varilla de aluminio. Hay muchos proveedores de tubos de acero inoxidable. Burns de acero inoxidable en California son probablemente los más conocidos. Pueden suministrar la mayoría de los grados de tubos de acero inoxidable ('U') y transiciones.
Cada vez que cortes un nuevo trozo de tubo, lo deslizarás por la varilla de aluminio hacia la brida de escape y la pegarás en su lugar. Tres pequeñas tachuelas espaciadas por el tubo igualmente mantendrán la articulación en su lugar. No se ajuste a ningún componente eléctrico durante la soldadura y, si es posible, retire las mangueras de freno trenzadas de acero inoxidable, así como la batería.
Debe cortar los tubos de acero inoxidable con precisión, particularmente los cortes a través de curvas. Estos cortes deben ser perpendiculares a la línea central de la tubería o el tubo. Un método simple para garantizar que el corte sea perpendicular es deslizar un anillo de goma ajustado sobre el tubo. El anillo de goma intentará ajustarse a la circunferencia más pequeña, y al hacerlo creará un borde perpendicular para seguir con un bolígrafo marcador.
Una vez que las piezas del tubo hayan sido cortadas, deben ser eliminadas. Una vez que hayan sido soldadas en su lugar, cualquier rebabas en el interior le dará una unión soldada para que los gases atraviesen.
Soldar los componentes
Una vez que todo el sistema de escape se ha agregado juntos, se puede quitar de la bicicleta para la soldadura final. Idealmente, el sistema de escape debe ser soldado por un soldador profesional. Aunque la apariencia de soldadura es importante, un soldador profesional también será consciente de la necesidad de minimizar la distorsión durante el proceso de soldadura, no tiene sentido hacer que un sistema perfectamente ajustado cuando se agregue solo para encontrar que no se ajusta a la bicicleta después de estar completamente soldado.